In London’s historic Canary Wharf, the mixed-use development Wood Wharf is an icon of sustainable construction. It is blazing a trail as one of the first projects in the UK to use Holcim’s low-carbon concrete ECOPact with 20% construction demolition materials inside.
500,000 m2 mixed-use development with offices, homes, retail and parks
One of the first UK projects to use concrete with 20% CDM - “ECOCycle® inside”
ECOPact gives at least 30% carbon reduction and 100% performance
Future use of pioneering carbon removal technology from neustark
Through Sivyer Logistics, Holcim is London’s largest recycler of CDM
2,500 tones of demolition concrete from North Quay recycled to be used in new building solutions
THE VISION
For over 30 years, Canary Wharf has shifted London’s center of gravity east and upwards, as technologies develop and ambition soars. Now Wood Wharf, a milestone in circular construction, is redefining this historic part of the city.
Canary Wharf has gained a reputation as a business district since the 1980s. Today, the 500,000 m2 master plan for Wood Wharf from Allies & Morrison and Glen Howells Architects is turning Canary Wharf into a thriving neighbourhood hub – with office spaces, thousands of homes, retail spaces and parks.
From the very start, our customer Canary Wharf Group (CWG) wanted to embed sustainability by design into its buildings, to create healthy, vibrant developments with nature inside that benefit everyone, and become net zero carbon as a group.
THE SOLUTIONs
Since building began in 2015, a cluster of iconic skyscrapers has grown as the centerpiece of Wood Wharf. Several of these are being built using Holcim’s ECOPact low-carbon custom concrete mixes that reduce CO2 by at least 30% while delivering 100% performance.
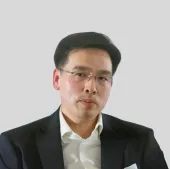
“The Holcim ECOPact range helped us focus on what low-carbon solutions and circularity options are available to us. As we progressed and our understanding and relationships with our supply chain partners grew, we were able to work closely to develop alternative concrete mixes.”
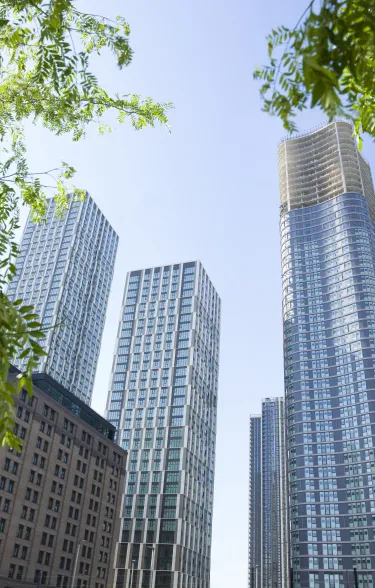
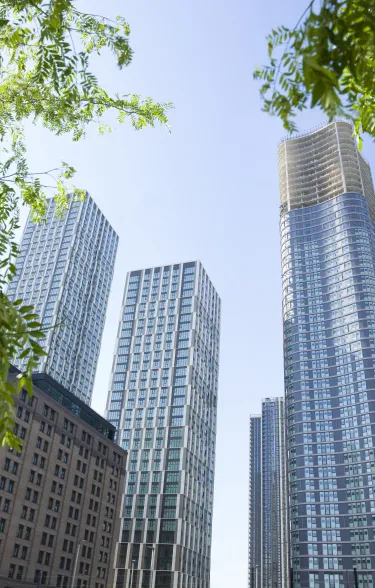
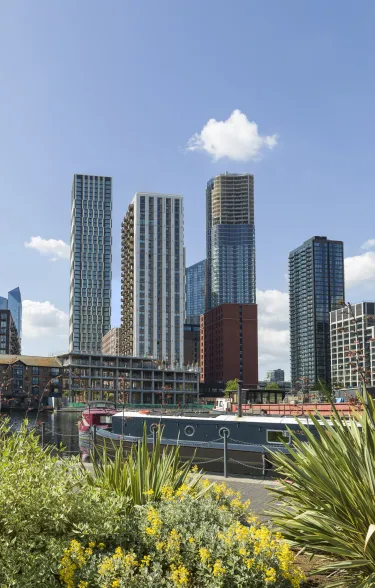
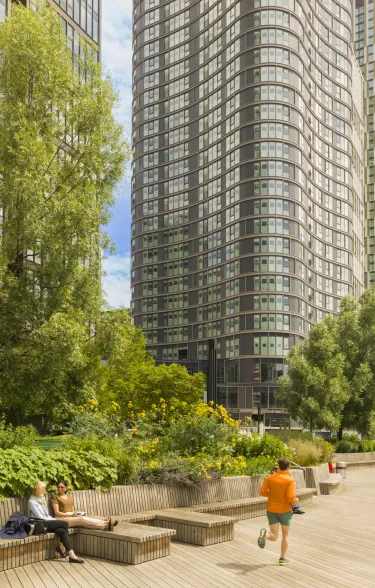
Breaking new ground in circularity
Jonathan and his team at CWG wanted to break new ground in the UK by driving circular construction to reduce waste and save primary materials. An approach made easier by the fact that London’s leaders want to make the city a global leader in circularity, with a policy framework that enables the use of construction demolition materials (CDM) in building.
From 2023, working closely with CWG and using its ECOCycle® technology, Holcim developed one of UK's first concretes with 20% recycled aggregates inside. Aggregates were taken from nearby North Quay – a decommissioned marine deck in Canary Wharf – then recycled for use in special concrete mixes.
“We could only have achieved this through the open and collaborative relationships with Holcim, who have helped us pioneer this new approach and embrace the art of what’s possible,” Jonathan explains.

The recycling took place at the Sivyer Logistics facility in nearby Greenwich, within sight of Wood Wharf’s gleaming skyscrapers. Here around 800,000 tons of CDM is recycled each year to create sustainable building solutions, using state-of-the-art recycling and recovery technologies.
Customer perspective
“As I walk through the Wood Wharf knowing the history behind it, the people involved in it. I feel it’s a great legacy for me to share with my children – to show them that they can do similarly incredible things with their future and their lives.”
Jonathan Ly, Director Structures, CWG
In another first, CWG will pioneer the use of a unique technology developed by carbon removal pioneer neustark and Holcim. This will involve ‘injecting’ biogenic CO2 into the remaining demolition concrete from North Quay for permanent storage using a special processing unit. This concrete will then be used to create innovative low-carbon concrete mixes for Wood Wharf.
Architect perspective
"The design decisions that we make, if we really look at the direct impact on the constructability of the building and the duration of the construction, we can unlock real potential for savings in waste and in carbon."
Shawn Duffy, Technical Principal at KPF
THE ICON
With 185,000 m2 of offices, 37,000 m2 of retail and community spaces and over 3,600 new homes, as well as over 3.6 hectares of public spaces, squares and parks, Wood Wharf is extending the Canary Wharf neighbourhood – as it flourishes as a hub for commerce, culture and living.
Motivated by CWG’s vision to “transform urban spaces into extraordinary environments”, Jonathan is proud to reflect upon what he and his team have achieved as they realize an inspirational and sustainable Building Icon in Wood Wharf.
Holcim perspective
"London is one of the world’s largest ‘urban mines’, and Sivyer Logistics is a leading player. We can take a customer’s CDM, recycle it onsite in Greenwich, then return it for use in new building solutions. This allowed Canary Wharf Group to achieve complete circularity at Wood Wharf."
Hear from Dan Thompson, Business Development Manager, Construction Demolition Materials, Aggregate Industries UK