“Our mission is to make London a global leader in circular construction” Pauline Metivier
To accelerate the shift to a circular economy, cities need to change their approach to construction demolition materials (CDM). As part of our commitment to decarbonize building, Holcim is driving circular construction in every metropolitan area where we operate.
Pauline Metivier, Head of Business Transformation and Sector Support at ReLondon, tells us how digital tools and the right policies can make this circular shift happen at scale, and shares some flagship initiatives from the UK capital.
What is ReLondon and how does it support circular construction?
ReLondon is a partnership between the Greater London Authority and the 33 London boroughs. Our mission is to make London a global leader in the circular economy. Our approach as a city to consumer materials is to lower the impact they have on both the climate and waste.
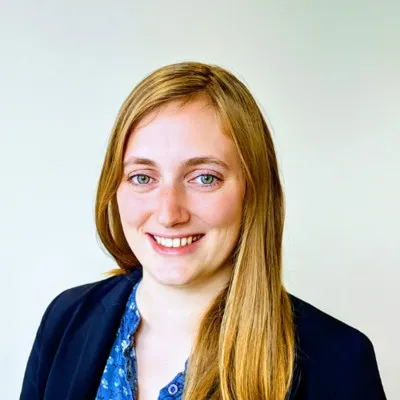
In London, construction materials and buildings are responsible for 10 percent of consumption-based emissions and nearly half of all waste generated. The focus is on encouraging reuse, retrofitting, and designing new buildings to be demountable and adaptable to reduce these environmental impacts.
How do you involve digital solutions in your strategy to improve circularity in the built environment?
We’re involved in three key flagship initiatives, and digitalization is part of all of them.
For example, we work very closely with the Greater London Authority on incorporating the Circular Economy Statement within the London Plan. This means helping those in charge of the big construction projects in London think about how they make their buildings circular. This can be done by using recycled or reused material, and by making the building easy to disassemble at the end of its life. That’s a leading global policy. We are proud of that as it is starting to make a difference in London.
The second thing is a business transformation program where we supported innovators in all sectors, but especially in the construction space, to help them develop a solution to facilitate material reuse and building adaptability.
Thirdly, ReLondon is part of a consortium of 31 organizations – which includes researchers, architects, engineers and other construction actors – from London, Copenhagen, Hamburg and the Helsinki region, which are working together on the Horizon 2020-funded ‘Circular Construction In Regenerative Cities’ (CIRCuIT) project.
Through the project, we are aiming to reduce the yearly consumption of virgin raw material by 20% in new constructions and show cost savings of 15% – helping the built environment deliver the Mayor’s commitment to making London a zero-carbon city by 2050.
We want to scale circular construction from niche applications that we see today to something that becomes the norm for the construction industry by building the evidence base and tools that both policymakers and construction companies need to incorporate those new principles into new developments. To this end, the project will produce a set of digital tools, including a data atlas, dashboard, citizen engagement portal, materials exchange platform and wiki, as well as a material stocks and flow database.
Wood Wharf, one of central London’s largest privately owned development sites, built with Holcim's low-carbon concrete with CDM inside
What challenges do we face when improving material flows in the built environment?
On one hand there is a lack of data. For example, it’s hard to know how much material is currently reused or recycled. It is our goal to develop this data.
On the other hand, the norm is still to demolish old buildings and build new ones using virgin raw materials. But really, what the norm should be is how you retrofit and reuse material instead of demolishing buildings. And that requires a huge change in how the industry operates and how policy makers develop their planning policies around it.
What are some of the best practices of government and industry collaboration to improve circularity?
The Circular Economy Statement is a leading policy in London that was developed in collaboration with industry. We will develop some practical guidance to help developers and architects incorporate circular principles into new building development.
That’s one of the key examples of how this collaboration works, and we want to continue that in the future. Currently, we are also developing a program that will be called “The London Circular Construction Coalition”. It will engage London boroughs and the Greater London Authority to further develop the planning policy, practices and infrastructure needed to enable that change. To really kick this initiative off we’re working very closely with industry players because this is how we can really make a change.
What do we need the most to accelerate the transition to a circular economy?
The first thing is infrastructure. We need physical space to store material to be reused. We need to connect demolition contractors with architects and developers so that materials can be easily reused from demolished buildings into new buildings.
The second thing is embedding those criteria into procurement tenders from both the public and private sectors. The market needs to drive this change, and it needs to be clear when you go out with a tender that you want a certain percentage of reused material or that you want your building to be designed to be demountable.
We need to build on the Circular Economy Statement that we have developed with the Greater London Authority. In the years to come, we need to strengthen this policy by making some criteria compulsory to really use the full planning powers that local authorities have.